In the high-demand world of manufacturing, where production schedules are tightly aligned with market needs, unplanned downtime is not just an inconvenience—it’s a direct threat to revenue and reputation.
For companies operating under these intense conditions, the benefits of 24/7 IT support for manufacturing has become a necessity.
Modern manufacturing relies heavily on complex networks of machinery, software, and communication systems. From robotic automation to IoT-enabled devices, these technologies have revolutionized the industry but also increased its dependency on seamless IT infrastructure.
Around-the-clock IT monitoring ensures these systems function optimally, minimizing downtime and maximizing productivity.
The Need for Reliable IT Support in Manufacturing
To appreciate the significance of 24/7 IT monitoring, one must first understand the critical role uptime plays in manufacturing. Uptime refers to the period during which a system or machine operates without failure. Even brief interruptions can cascade into delayed production schedules, missed delivery deadlines, and substantial financial losses.
For example, a 2019 survey by ITIC revealed that an hour of downtime can cost companies up to $300,000 on average. In manufacturing, this figure can escalate due to the sheer scale of production processes, making uninterrupted IT support indispensable.
However, maintaining high uptime is easier said than done.
Common Challenges in Manufacturing IT Support
Manufacturing companies face numerous IT-related challenges that threaten productivity:
-
Aging Infrastructure: Many manufacturing plants still rely on outdated systems that struggle to keep up with modern demands. These legacy systems are more prone to failures and incompatible with emerging technologies.
-
Cybersecurity Risks: Increasing digitization has made manufacturing systems attractive targets for cyberattacks. Ransomware and malware can bring production to a standstill.
-
Complex Systems Integration: With various tools and platforms working together, integration issues can lead to inefficiencies and breakdowns.
-
Limited In-House Expertise: Many manufacturers lack the internal IT resources needed to monitor and address these challenges effectively.
How 24/7 IT Support for Manufacturing Helps Address Challenges
Continuous IT monitoring provides a proactive approach to preventing downtime and resolving problems before they escalate. Unlike reactive support that waits for issues to arise, 24/7 IT services actively track system performance to detect anomalies early.
Benefits of Continuous IT Monitoring
-
Real-Time Alerts: Instant notifications of system errors allow IT teams to act swiftly, minimizing the impact of potential failures.
-
Routine Health Checks: Regular evaluations of infrastructure identify vulnerabilities and ensure all systems remain operational.
-
Proactive Problem Resolution: With round-the-clock monitoring, IT experts can often resolve issues before they become noticeable to users.
For example, a manufacturing plant that uses managed IT services can expect a significant reduction in downtime after implementing real-time monitoring, demonstrating the tangible benefits of a proactive approach
Boosting Employee Productivity with Reliable Outsourced IT Support
The effects of uninterrupted IT support extend beyond machinery and systems. Employees also benefit significantly from stable IT environments, leading to higher morale and productivity.
Key Advantages for Employees
-
Reduced Downtime Stress: Employees can focus on their tasks without disruptions caused by system failures.
-
Streamlined Processes: Automated troubleshooting and quick IT resolutions eliminate delays in workflows.
-
Greater Confidence: Knowing that IT systems are continuously monitored fosters trust in the organization’s infrastructure.
By empowering employees with reliable tools and resources, manufacturers can optimize their workforce’s efficiency and satisfaction.
The Long-Term ROI of 24/7 IT Support for Manufacturing
While investing in continuous IT support may seem costly upfront, the long-term financial benefits far outweigh the expenses.
-
Minimized Downtime Costs: With reduced interruptions, companies save on lost production and labor expenses.
-
Extended Equipment Lifespan: Regular IT maintenance prevents wear and tear on technology, delaying costly replacements.
-
Improved Efficiency: Optimized workflows and fewer disruptions lead to higher output and profitability.
Moreover, manufacturers that adopt 24/7 IT support gain a competitive edge by ensuring consistent delivery of high-quality products on schedule.
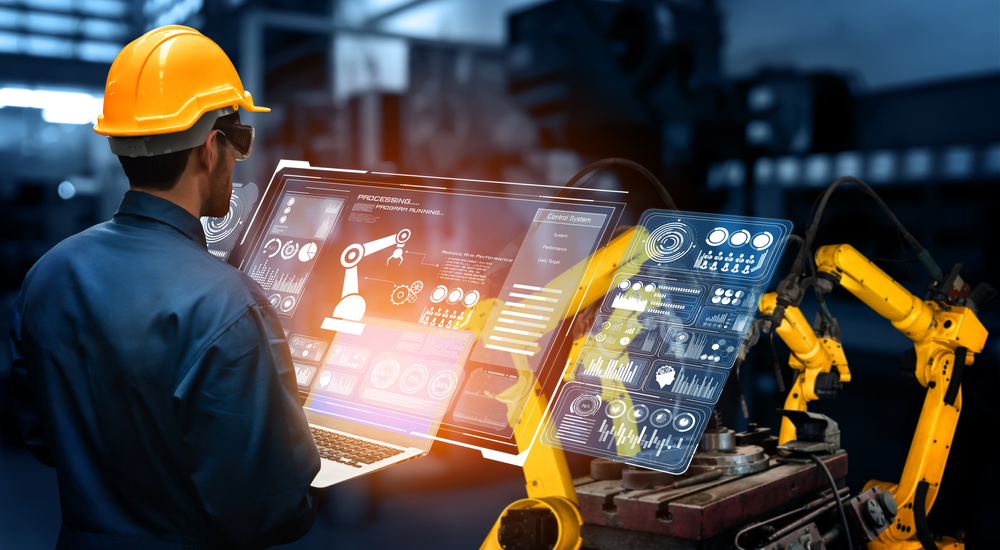
Emerging Technologies and the Future of IT Support
As technology evolves, so do the demands on IT systems in manufacturing. Innovations like artificial intelligence (AI) and machine learning are poised to revolutionize how manufacturing operations are monitored and optimized.
- AI for Predictive Maintenance: AI algorithms can predict when equipment is likely to fail, allowing for preemptive repairs that prevent downtime.
- IoT Integration: Internet of Things (IoT) devices enable real-time data collection and analysis, enhancing decision-making processes.
- Cloud Solutions: Cloud-based systems offer scalability and flexibility, ensuring manufacturers can adapt to changing demands.
By staying ahead of these trends, manufacturers can future-proof their operations and continue to thrive in a rapidly changing industry.
Taking the Next Step Toward Maximizing Uptime
In the competitive manufacturing sector, downtime is not an option. Investing in 24/7 IT support ensures systems run smoothly, productivity remains high, and costly disruptions are minimized.
At Be Structured, we specialize in providing reliable 24/7 IT support tailored to the unique needs of manufacturing companies. From proactive monitoring to expert integration of cutting-edge technologies, our services are designed to help you maximize uptime and productivity.
Take the first step toward uninterrupted operations—schedule a free consultation today!